Manganstahl, auch Hadfield-Stahl oder Mangaloy genannt, dient der Verbesserung von FESTIGKEIT, HALTBARKEIT und ZÄHIGKEIT, d. Der allgemeine und für alle Anwendungen am häufigsten verwendete Mangangehalt beträgt 13 %, 18 % und 22 %.
Aber wissen Sie, was der Unterschied zwischen ihnen ist?
Hier stellen wir Ihnen die wichtigsten Mangan-Typen kurz vor.
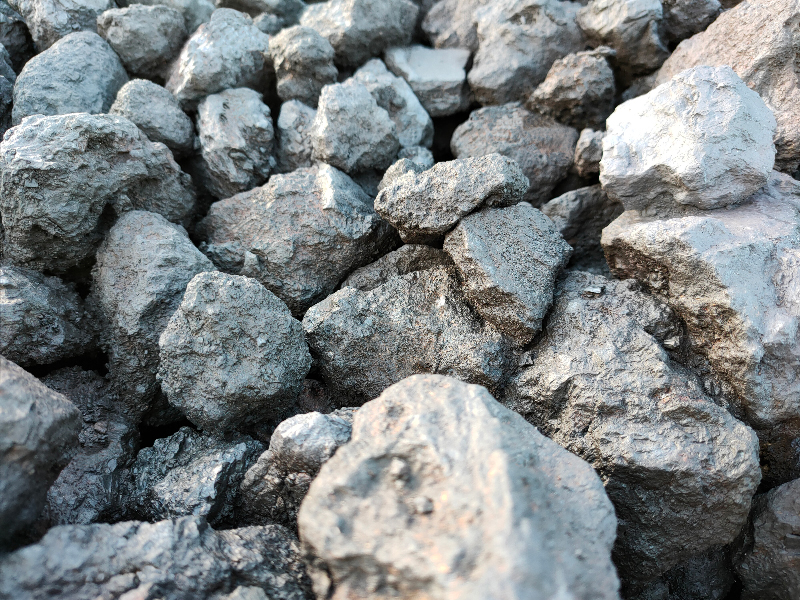
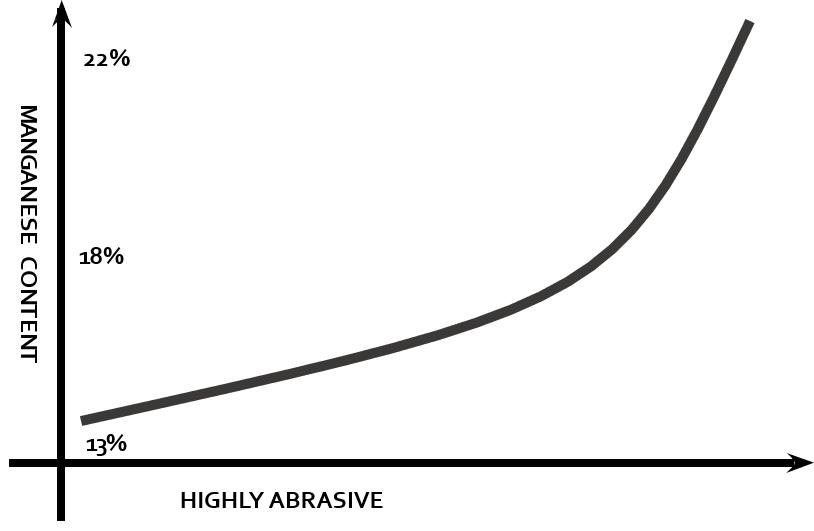
1、13% MANGAN
Der Standard umfasst 12-14 % Mangan. Es ist für den Einsatz in weichen Anwendungen mit geringem Abrieb erhältlich, insbesondere für mittelstarkes und nicht abrasives Gestein sowie weiche und nicht abrasive Materialien.
Das Hauptmerkmal dieses Produkts ist seine hohe Verschleiß- und Widerstandsfähigkeit
Starke Abnutzung der Oberfläche wirkt sich verfestigend auf das austenitische Gefüge dieses Stahls aus. In Kombination mit dem Kohlenstoffgehalt gemäß den internationalen Standards führt dies zu einer Erhöhung der Härte von 200 BHN (in der gelieferten Platte) auf eine Betriebshärte von mindestens 600 BHN.
Diese Kaltverfestigungsfähigkeit erneuert sich während der gesamten Nutzungsdauer. Die nicht kaltverfestigten Unterschichten weisen eine hervorragende Schlagfestigkeit und eine sehr hohe Duktilität auf.
2、18 % MANGAN
18 % Mangan-Verschleißteile liegen im Mittelfeld. Es ist standardmäßig für alle Backen- und Kegelbrecher geeignet. Fast für alle Gesteinsarten geeignet, jedoch nicht für harte und abrasive Materialien.
3、22 % MANGAN
Eine Option für alle Backen- und Kegelbrecher.
Besonders schnelle Kaltverfestigung bei abrasiven Anwendungen, besser geeignet für harte und (nicht) abrasive sowie mittelstarke und abrasive Materialien. Verschleißteile mit 22-24 % Mangan stellen das obere Ende des Spektrums dar. Bei diesem Mangangehalt sind Verschleißteile spröde und eignen sich daher nur für Materialien mit hohem Abrieb, die noch spröder sind.
Wie auch immer, die Wahl der richtigen Mangan-Verschleißteile ist immer die beste Zerkleinerungslösung.
Wenn Sie Unterstützung benötigen, stehen wir Ihnen jederzeit zur Verfügung.
Zeitpunkt der Veröffentlichung: 26. Juli 2023