Zu viele Unternehmen investieren nicht genug in die Wartung ihrer Geräte, und das Ignorieren von Wartungsproblemen führt nicht dazu, dass die Probleme verschwinden.
„Laut führenden Zuschlagstoffherstellern machen Reparaturen und Wartungsarbeiten durchschnittlich 30 bis 35 Prozent der direkten Betriebskosten aus“, sagt Erik Schmidt, Resource Development Manager bei Johnson Crushers International, Inc. „Das ist ein ziemlich großer Faktor für die Gemeinkosten dieser Ausrüstung.“
Wartung ist oft einer der Punkte, die gekürzt werden, aber ein unterfinanziertes Wartungsprogramm wird den Betrieb später viel Geld kosten.
Es gibt drei Wartungsansätze: reaktiv, präventiv und vorausschauend. Reactive repariert etwas, das fehlgeschlagen ist. Vorbeugende Wartung wird oft als unnötig angesehen, minimiert aber Ausfallzeiten, da die Maschine vor dem Ausfall repariert wird. Vorausschauend bedeutet, anhand historischer Lebensdauerdaten zu bestimmen, wann eine Maschine wahrscheinlich ausfallen wird, und dann die notwendigen Schritte zu unternehmen, um das Problem zu beheben, bevor es zu einem Ausfall kommt.
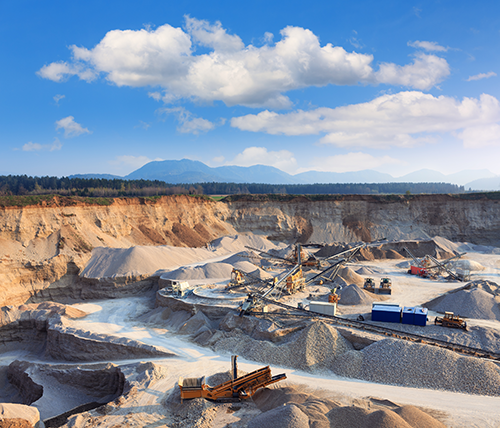
Um Maschinenausfällen vorzubeugen, gibt Schmidt Tipps zu Horizontalwellenprallbrechern (HSI) und Kegelbrechern.
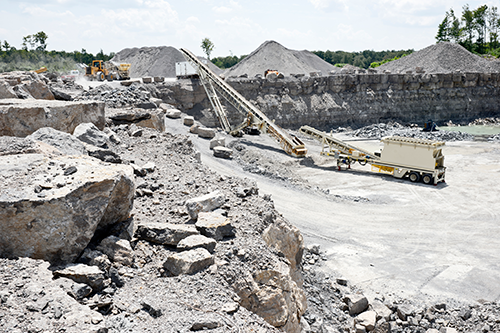
Führen Sie tägliche Sichtprüfungen durch
Laut Schmidt werden tägliche Sichtprüfungen die überwiegende Mehrheit der drohenden Ausfälle aufdecken, die den Betrieb durch unnötige und vermeidbare Ausfallzeiten kosten könnten. „Deshalb steht es auf Platz eins meiner Tipps zur Brecherwartung“, sagt Schmidt.
Zu den täglichen Sichtprüfungen an HSI-Brechern gehört die Überwachung wichtiger Verschleißteile des Brechers, wie Rotor und Auskleidungen, sowie Benchmark-Elemente, wie Ausrollzeiten und Stromaufnahme.
„Der Mangel an täglichen Kontrollen ist weitaus größer, als man zugeben möchte“, sagt Schmidt. „Wenn Sie jeden Tag in die Brechkammer gehen und nach Verstopfungen, Materialansammlungen und Verschleiß suchen, können Sie Ausfälle verhindern, indem Sie zukünftige Probleme schon heute erkennen. Und wenn Sie in wirklich nassem, klebrigem oder lehmigem Material arbeiten, müssen Sie möglicherweise mehr als einmal am Tag hinein.
Visuelle Kontrollen sind von entscheidender Bedeutung. In dem Fall, dass das Förderband unter einem Kegelbrecher blockiert, sammelt sich das Material in der Brechkammer an und blockiert schließlich den Brecher. Es kann Material im Inneren stecken bleiben, das nicht sichtbar ist.
„Niemand kriecht da rein, um zu sehen, dass es noch im Kegel verstopft ist“, sagt Schmit. „Sobald sie das Austragsband wieder in Gang bringen, starten sie den Brecher. Das ist absolut falsch. Aussperren und markieren, dann reingehen und nachschauen, denn Material kann leicht Kammern blockieren, was zu übermäßigem Verschleiß und sogar Folgeschäden am Anti-Schleuder-Mechanismus oder zugehörigen internen Komponenten führen kann.
Missbrauchen Sie Ihre Maschinen nicht
Maschinen über ihre Grenzen hinaus zu treiben oder sie für Anwendungen zu verwenden, für die sie nicht ausgelegt sind, oder das Unterlassen bestimmter Maßnahmen sind Formen des Missbrauchs der Maschine. „Alle Maschinen, egal vom Hersteller, haben Grenzen. Wenn man sie über ihre Grenzen hinaustreibt, ist das Missbrauch“, sagt Schmidt.
Eine häufige Form des Missbrauchs bei Kegelbrechern ist das Aufschwimmen der Schüssel. „Auch Ring-Bounce oder Upper-Frame-Bewegung genannt. Es ist das Entlastungssystem der Maschine, das dafür ausgelegt ist, dass nicht zerbrechliche Materialien durch die Maschine gelangen können. Wenn Sie jedoch aufgrund der Anwendung ständig Entlastungsdrücke überwinden, führt dies zu Schäden am Sitz und anderen internen Komponenten. Es ist ein Zeichen von Missbrauch und das Endergebnis sind teure Ausfallzeiten und Reparaturen“, sagt Schmidt.
Um ein Aufschwimmen der Schüssel zu vermeiden, empfiehlt Schmidt, dass Sie das in den Brecher gelangende Aufgabematerial überprüfen, aber die Drossel des Brechers weiterhin mit Strom versorgen. „Möglicherweise gelangen zu viele Feinteile in den Brecher, was bedeutet, dass Sie ein Siebproblem haben – kein Zerkleinerungsproblem“, sagt er. „Außerdem möchten Sie den Brecher mit Drossel beschicken, um maximale Produktionsraten und eine 360-Grad-Zerkleinerung zu erzielen.“ Beschicken Sie den Brecher nicht rieselfähig; Dies führt zu ungleichmäßigem Komponentenverschleiß, unregelmäßigeren Produktgrößen und einer geringeren Produktion. Ein unerfahrener Bediener wird oft lieber die Vorschubgeschwindigkeit reduzieren, als einfach die Schließseiteneinstellung zu öffnen.
Für HSI empfiehlt Schmidt, dem Brecher eine gut abgestufte Zufuhr zuzuführen, da dies die Produktion maximiert und gleichzeitig die Kosten minimiert, und die Zufuhr beim Zerkleinern von recyceltem Beton mit Stahl richtig vorzubereiten, da dadurch ein Verstopfen der Kammer und ein Brechen der Schlagleiste reduziert werden. Die Nichtbeachtung bestimmter Vorsichtsmaßnahmen bei der Verwendung von Geräten ist missbräuchlich.
Verwenden Sie die richtigen und sauberen Flüssigkeiten
Verwenden Sie immer die vom Hersteller vorgeschriebenen Flüssigkeiten und prüfen Sie deren Richtlinien, wenn Sie vorhaben, etwas anderes als das, was angegeben ist, zu verwenden. „Seien Sie vorsichtig, wenn Sie die Ölviskosität ändern. Dadurch ändert sich auch die EP-Einstufung (Extreme Pressure) des Öls und es kann sein, dass es in Ihrer Maschine nicht mehr die gleiche Leistung erbringt“, sagt Schmidt.
Schmidt warnt außerdem davor, dass Großöle oft nicht so sauber sind, wie Sie denken, und empfiehlt Ihnen, Ihr Öl analysieren zu lassen. Erwägen Sie eine Vorfiltration an jedem Übergangs- oder Wartungspunkt
Auch Verunreinigungen wie Schmutz und Wasser können in den Kraftstoff gelangen, sei es bei der Lagerung oder beim Befüllen der Maschine. „Die Zeiten des offenen Eimers sind vorbei“, sagt Schmidt. Heutzutage müssen alle Flüssigkeiten sauber gehalten werden und es wird viel mehr Vorsicht geboten, um eine Kontamination zu vermeiden.
„Tier-3- und Tier-4-Motoren verwenden ein Hochdruck-Einspritzsystem, und wenn Schmutz in das System gelangt, ist er ausgelöscht. Am Ende müssen Sie die Einspritzpumpen der Maschine und möglicherweise alle anderen Kraftstoffverteilerkomponenten im System austauschen“, sagt Schmidt.
Eine falsche Anwendung erhöht die Wartungsprobleme
Eine falsche Anwendung führt laut Schmidt zu vielen Reparaturen und Ausfällen. „Schauen Sie sich an, was da reinkommt und was Sie davon erwarten. Was ist das größte Zufuhrmaterial, das in die Maschine gelangt, und welche Einstellung hat die Maschine auf der geschlossenen Seite? Daraus ergibt sich das Untersetzungsverhältnis der Maschine“, erklärt Schmidt.
Bei HSIs empfiehlt Schmidt, ein Untersetzungsverhältnis von 12:1 bis 18:1 nicht zu überschreiten. Zu hohe Reduktionsverhältnisse reduzieren die Produktionsraten und verkürzen die Lebensdauer des Brechers.
Wenn Sie die Leistung eines HSI- oder Kegelbrechers in seiner Konfiguration überschreiten, müssen Sie damit rechnen, dass sich die Lebensdauer bestimmter Komponenten verkürzt, da Sie Teile der Maschine belasten, die nicht für diese Belastung ausgelegt sind.
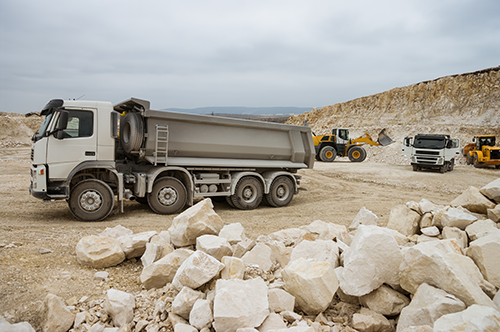
Eine falsche Anwendung kann zu ungleichmäßigem Linerverschleiß führen. „Wenn sich der Brecher unten in der Kammer oder oben in der Kammer abnutzt, entstehen Taschen oder Haken, und es kommt zu einer Überlastung, entweder zu hoher Stromaufnahme oder zum Aufschwimmen der Schüssel.“ Dies wirkt sich negativ auf die Leistung aus und führt zu langfristigen Schäden an den Komponenten.
Benchmarking wichtiger Maschinendaten
Die Kenntnis der normalen oder durchschnittlichen Betriebsbedingungen einer Maschine ist für die Überwachung des Maschinenzustands von entscheidender Bedeutung. Schließlich können Sie nicht wissen, wann eine Maschine außerhalb der normalen oder durchschnittlichen Betriebsbedingungen arbeitet, es sei denn, Sie kennen diese Bedingungen.
„Wenn man ein Logbuch führt, bilden langfristige Betriebsleistungsdaten einen Trend, und alle Daten, die von diesem Trend abweichen, könnten ein Indikator dafür sein, dass etwas nicht stimmt“, sagt Schmidt. „Möglicherweise können Sie vorhersagen, wann eine Maschine ausfallen wird.“
Sobald Sie genügend Daten protokolliert haben, können Sie Trends in den Daten erkennen. Sobald Sie sich der Trends bewusst werden, können Sie Maßnahmen ergreifen, um sicherzustellen, dass diese nicht zu ungeplanten Ausfallzeiten führen. „Wie lang sind die Auslaufzeiten Ihrer Maschinen?“ fragt Schmidt. „Wie lange dauert es, bis der Brecher zum Stillstand kommt, nachdem Sie den Stoppknopf gedrückt haben? Normalerweise dauert es beispielsweise 72 Sekunden; Heute hat es 20 Sekunden gedauert. Was sagt dir das?“
Durch die Überwachung dieser und anderer potenzieller Indikatoren für den Maschinenzustand können Sie Probleme früher erkennen, bevor die Ausrüstung während der Produktion ausfällt, und die Wartung kann für einen Zeitraum geplant werden, der Sie mit geringen Ausfallzeiten belastet. Benchmarking ist der Schlüssel zur Durchführung einer vorausschauenden Wartung.
Eine Unze Vorbeugung ist ein Pfund Heilung wert. Reparaturen und Wartung können kostspielig sein, aber angesichts aller potenziellen Probleme, die sich daraus ergeben, dass sie nicht behoben werden, ist dies die kostengünstigere Option.
Zeitpunkt der Veröffentlichung: 09.11.2023